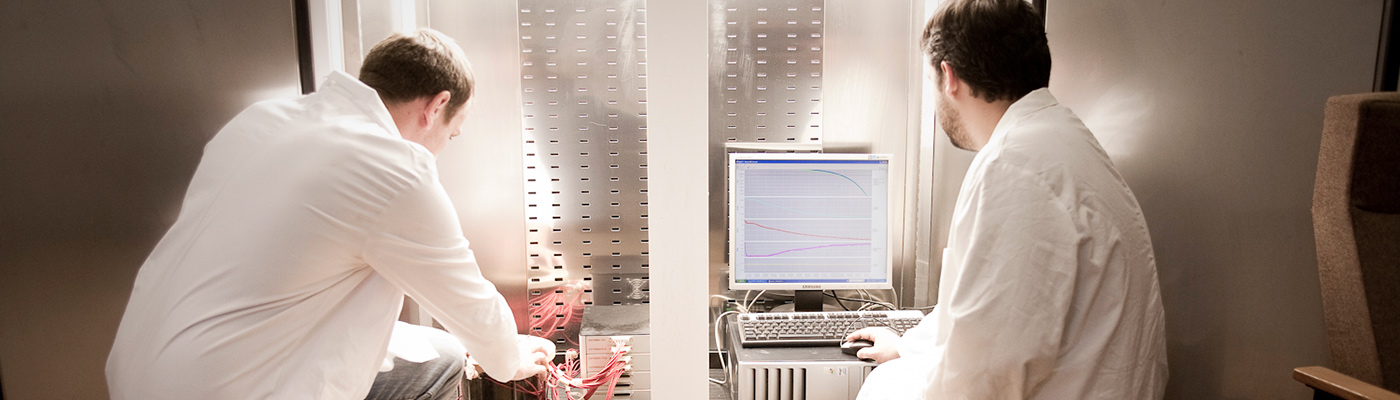
Research themes
Our research is focused on solving the challenges we face today and is grouped into five different themes that overlap and support each other.
Covering topics as broad as advanced functional materials and robotics for extreme environments, our research takes advantage of the University's modern facilities - as well as our collaborations with centres and institutes - to produce truly outstanding work.
Explore each of the themes and the areas in which our staff specialise below.
Advanced functional materials and devices
Applied research, ranging from atomic-level to devices leading to new technology development.
Electronic engineering for agriculture
Research into the many different uses of electronics in agriculture technologies.